What is a dead band?
The dead band is the range through which an input can change without triggering an observable response.
Deadband can be used in control systems such as servo amplifiers to avoid oscillation or frequent on-off cycles (called “hunting” in proportional control systems).
The control valve behaves with dead band such that there may be some kind of resistance or feedback between the controller output and the actual position of the stem in the valve actuator.
When the controller output direction changes at any moment
Deadband in the system may be caused by mechanical gaps caused by physical gaps between parts with mechanical slack or play in mechanical joints.
A dead band may also be caused by:
Excessive valve friction
Improperly sized actuator
itopi positioner is defective and…
This problem is more in rotary valves due to the design of rotary actuator and shaft coupling, and it is necessary to convert it into rotary motion.
Shaft torsion occurs in rotary valves where the drive shaft is twisted.
Due to the high friction of the sealing surface, the ball or disc gets stuck and does not rotate to open and close.
Finally, the ball or disc is released.
How is the dead band created in the control valve?
Dead band occurs in a control valve due to closed friction, unbalanced forces and some other factors in the control valve assembly.
The control valve dead band is the range that a measured signal can change without initiating a response from the actuator.
The dead band concept for forward and reverse valve control actuators is shown in the schematic diagram below.
Dead band concept for direct and reverse control valve actuation
Each valve control actuator is built with a fixed spring.
A dead band is attached to the fixed spring in the valve actuator.
Dead band affects valve control performance during automatic loop control.
The tolerance of the control loop for the dead band varies greatly depending on the response of that loop.
An increasing or widening dead band in a control valve produces a slow or slow flow control response.
Some common symptoms of increased deadband include:
There is no movement in the control valve after the controller starts the control movement.
Oscillating movements of the valve control during the automatic control of the loop
How do you determine the deadband control valve?
Understanding the concept of dead band helps in troubleshooting process control loop problems.
Increasing the deadband results in a slower control response of the system.
So we have an idea of the dead band level in a control valve that is at the heart of a critical process operation.
Connect a 0 to 60 psi pressure source to the valve control actuator in the range setting on the valve.
The method of determining the dead band and the adjustment range of the control valve bench is shown below:
Dead band calculation method
Disconnect the valve control from operation and apply supply pressure.
The given source pressure should be close to the lower set pressure range.
Now gradually increase the pressure until the stroke of the valve reaches the middle of the indicator, which is almost in the middle of the travel.
In the pressure reading, make sure that it is P1, which is shown on the PG pressure gauge.
Now gradually reduce the pressure until the valve travel reaches the initial position of the valve travel.
Note this pressure value as P2 shown on the PG pressure gauge.
Now subtract both P1 and P2 pressure values to get a dead band in psi.
Here the dead band is the difference between the two pressures P1 and P2.
and measured on the PSI scale. Finally, calculate the dead band percentage using the range relationship.
Control valve assemblies are the main source of dead band in instrumentation and control loops, which is caused by friction, backlash, shaft blowout, relay valve or spool dead band, etc.
Deadband is a general phenomenon where controller output range values do not change the measured value or process variable (PV) when the direction of the input signal is reversed.
The process variable (PV) deviates from the set point during the load disturbance.
This deflection initiates a required action through the controller and returns during the process.
A change in the controller output does not affect the process variable, meaning it does not produce any corresponding corrective change in the process variable.
But the change in the process variable only occurs if there is a maximum change in the controller output to progress in the dead band.
The controller can reverse or change its direction at any time, but the controller signal must flow through the deadband before any corrective change in the process variable can occur.
The measured value in the process is confirmed by the presence of the dead band.
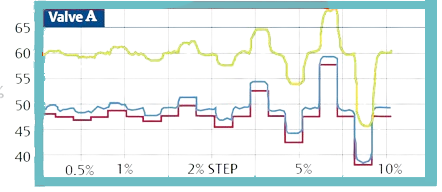